Yes, exhaust manifold bolts are special because they are designed to withstand extreme temperatures, resist corrosion, and endure constant vibrations from the engine. Unlike regular bolts, they are often made from high-strength materials like stainless steel or Inconel to prevent loosening, breaking, or rusting in harsh conditions.
Exhaust manifold bolts might seem like ordinary hardware components at first glance, but they play a critical role in the overall functioning and efficiency of a vehicle’s exhaust system. The exhaust manifold, which collects the gases from the engine cylinders and directs them into the exhaust pipe, is subject to extreme temperatures, vibrations, and pressure. The bolts that secure the manifold to the engine block are designed to withstand these harsh conditions, making them far from ordinary.
Contents
Why Are Exhaust Manifold Bolts Special?
Exhaust manifold bolts are crucial for several reasons:
- High-Temperature Resistance: The exhaust manifold operates at extremely high temperatures, often exceeding 1200°F (650°C). Regular bolts are not designed to endure these temperatures without degrading or losing their tensile strength. Exhaust manifold bolts are usually made of materials that can withstand this heat without stretching, breaking, or corroding.
- Corrosion Resistance: Exhaust manifolds are exposed to constant thermal cycling and various contaminants, such as moisture, road salt, and chemicals. These conditions can lead to rust and corrosion. Exhaust manifold bolts are often coated or made from stainless steel, titanium, or other alloys that offer better resistance to corrosion.
- Vibration Resistance: The engine produces vibrations that can cause regular bolts to loosen over time. Exhaust manifold bolts are designed with higher clamping forces and specific thread patterns to resist loosening caused by these vibrations.
- Thermal Expansion Compensation: Metals expand and contract with temperature changes. Exhaust manifold bolts are designed to accommodate the thermal expansion of the manifold and the engine block, preventing warping or cracking of the manifold.
- Shear Strength: Exhaust manifold bolts need to be strong enough to resist shearing forces. The bolts must handle not only the weight of the manifold but also the forces generated by engine vibrations, exhaust gas pressure, and thermal expansion.
Types of Exhaust Manifold Bolts
There are several types of exhaust manifold bolts, each with specific characteristics to suit different applications:
- Standard Steel Bolts: These are the most common and cost-effective type. They are often coated with zinc or other rust-resistant materials to prevent corrosion. However, they may not be the best choice for high-performance or racing applications due to their limited high-temperature tolerance.
- Stainless Steel Bolts: These bolts offer superior corrosion resistance, making them ideal for vehicles exposed to harsh environments, such as salty coastal areas or regions with heavy winter road treatments. They have decent high-temperature resistance but may not match the strength of other materials like Inconel or titanium.
- Inconel Bolts: Inconel is a high-performance alloy known for its excellent resistance to high temperatures, corrosion, and oxidation. It is commonly used in racing and high-performance vehicles due to its superior durability under extreme conditions. However, Inconel bolts are expensive and may not be necessary for standard vehicles.
- Titanium Bolts: Titanium bolts are lightweight, corrosion-resistant, and have good high-temperature tolerance. They are often used in high-performance applications where reducing weight is critical. However, they are also expensive and can be prone to galling (metal surface damage caused by adhesion during tightening).
- Studs and Nuts: Instead of traditional bolts, some exhaust manifolds use studs that are screwed into the engine block with nuts to secure the manifold. This configuration allows for easier removal and replacement, as the studs remain in the block, reducing the risk of thread damage.
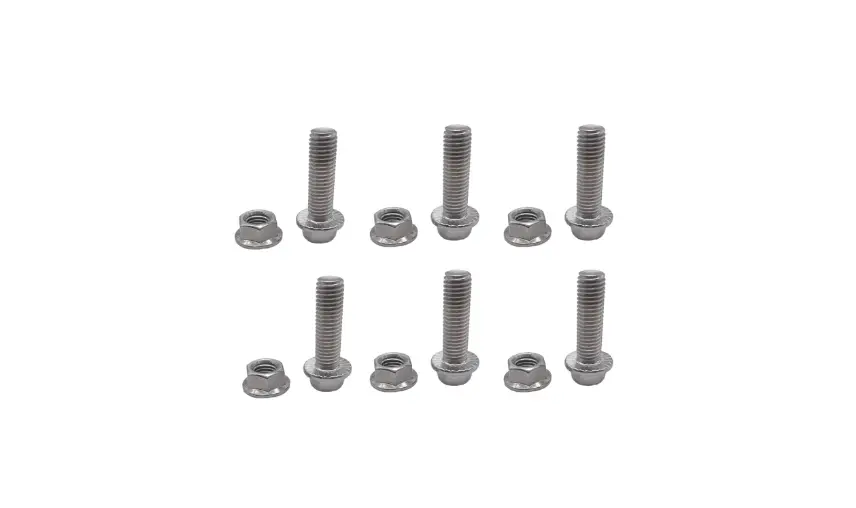
Installing and Replacing Exhaust Manifold Bolts
Follow the steps below to install the exhaust manifold bolts –
- Use the Correct Bolts: Always use the manufacturer-recommended bolts for your specific vehicle. Using the wrong type can lead to issues like loosening, corrosion, or even manifold damage.
- Apply Anti-Seize Compound: Applying a high-temperature anti-seize compound to the threads of the bolts can help prevent galling, corrosion, and make future removal easier. Be careful not to overapply, as excess compound can contaminate the exhaust system.
- Torque Bolts to Specification: Use a torque wrench to tighten the bolts to the manufacturer’s recommended specifications. Over-tightening can cause thread damage or bolt breakage, while under-tightening can lead to exhaust leaks.
- Inspect for Damage: Before installation, inspect both the bolts and the manifold for any signs of damage, corrosion, or wear. Replace any damaged components to ensure a proper seal.
- Use New Bolts When Necessary: It’s a good practice to replace old exhaust manifold bolts with new ones whenever the manifold is removed. Reusing old bolts, especially if they are rusted or corroded, increases the risk of breakage.
- Heat Cycling: Some bolts may require a specific heat cycling process after installation, which involves running the engine to operating temperature and then allowing it to cool. This helps seat the manifold properly and ensures bolt tension is correct.
Frequently Asked Questions
Here are some FAQs about exhaust manifold bolts –
- Are exhaust manifold bolts different from regular bolts?
Yes, exhaust manifold bolts are designed to withstand extreme temperatures, resist corrosion, endure vibrations, and compensate for thermal expansion. Regular bolts do not have these properties and are not suitable for use in exhaust systems. - Can I reuse old exhaust manifold bolts?
It is generally recommended to use new bolts whenever the exhaust manifold is removed. Reusing old bolts can increase the risk of breakage, loosening, or corrosion, which can lead to exhaust leaks and other issues. - What material is best for exhaust manifold bolts?
The best material depends on the specific application. For most standard vehicles, stainless steel or coated steel bolts are sufficient. For high-performance or racing applications, Inconel or titanium bolts may be preferred due to their superior heat and corrosion resistance. - Why do exhaust manifold bolts break?
Exhaust manifold bolts can break due to high temperatures, vibrations, rust, or improper installation (such as over-tightening or cross-threading). Age and exposure to harsh conditions can also make them brittle over time. - How can I prevent exhaust manifold bolts from loosening?
To prevent bolts from loosening, use the correct type of bolts, apply a high-temperature anti-seize compound, and torque them to the manufacturer’s specifications. Additionally, using bolts with specific thread designs or lock washers can help resist loosening due to vibrations.
Conclusion
Exhaust manifold bolts are indeed special and play a critical role in maintaining the performance and reliability of your vehicle’s exhaust system. They must endure extreme temperatures, resist corrosion, and withstand vibrations without loosening or breaking.