To rebuild an engine, follow these steps: disassemble the engine, inspect all parts for damage or wear, replace any faulty components, reassemble the engine with new gaskets and seals, and properly torque all bolts to specifications. Rebuilding an engine involves a thorough process of taking apart the engine, examining each part for any signs of damage or wear, and replacing any faulty components.
Rebuilding an engine can be one of the most rewarding experiences for car enthusiasts and mechanics alike. It’s a challenging process that requires patience, precision, and the right tools, but it can breathe new life into a vehicle that would otherwise be scrapped. This comprehensive guide will walk you through the basic steps involved in rebuilding an engine, ensuring that even those with minimal experience can follow along.
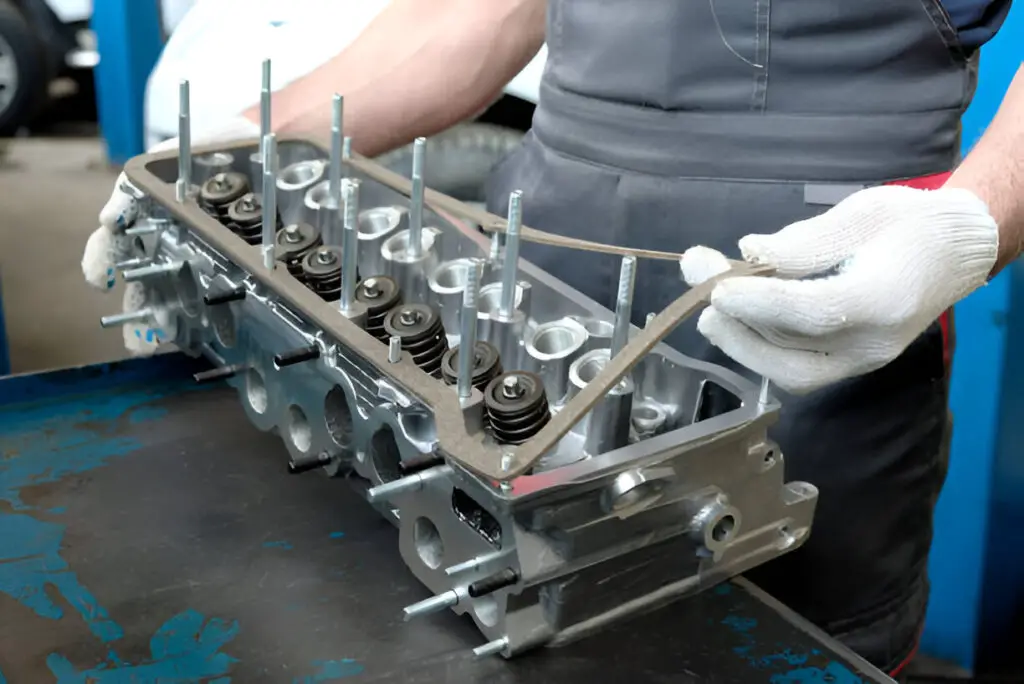
Contents
What Does It Mean to Rebuild an Engine?
Rebuilding an engine involves disassembling it, cleaning and inspecting its parts, and replacing worn components to restore it to like-new condition. This differs from simply repairing a broken engine, as it involves working with the engine’s core components, such as the pistons, crankshaft, bearings, gaskets, and seals. Rebuilding can extend the life of an engine, improve performance, and save money compared to purchasing a new or remanufactured engine.
When Should Consider Rebuilding an Engine?
There are several reasons why you might rebuild an engine:
- High Mileage: Engines wear down after long periods of use, particularly beyond 150,000 miles. A rebuild can help prevent major failures and improve longevity.
- Burning Oil or Coolant: Leaks or consumption of oil or coolant may signal internal engine issues.
- Loss of Compression: This could be due to worn-out piston rings or cylinder walls, leading to a significant decrease in power and fuel efficiency.
- Engine Knocking or Ticking: Unusual noises can point to bearing or valve issues that need attention.
- Frequent Overheating: Overheating may damage internal components, necessitating a rebuild.
How to Rebuild an Engine
Before starting the rebuild, ensure you have the following tools and materials on hand:
- Basic hand tools (wrenches, sockets, screwdrivers)
- Torque wrench for precise tightening
- Engine hoist to lift the engine from the vehicle
- Engine stand to hold the engine while you work
- Micrometer and dial bore gauge for measuring tolerances
- Piston ring compressor
- Engine rebuild kit (includes gaskets, seals, bearings, and sometimes pistons and rings)
- Replacement parts (pistons, valves, crankshaft, etc., as needed)
- Cleaning supplies (degreaser, wire brushes)
- Assembly lube and engine oil
Step-by-Step Guide to Rebuilding an Engine
Rebuilding an engine is a challenging but rewarding process that requires attention to detail, proper tools, and a systematic approach. Below is a step-by-step guide to help you rebuild your engine effectively.
1. Remove the Engine from the Vehicle
The first step in rebuilding an engine is removing it from the vehicle. This process varies depending on the car’s make and model, but it generally involves disconnecting the battery, draining the fluids, disconnecting hoses and electrical connections, and unbolting the engine mounts. An engine hoist is essential for safely removing the engine from the vehicle.
2. Disassemble the Engine
Once the engine is out of the vehicle, start by disassembling it. This involves removing the valve covers, cylinder heads, intake and exhaust manifolds, timing components, oil pan, and pistons. Keep track of all the parts and their respective locations, labeling them if necessary. Be careful not to damage any parts that you intend to reuse.
Tips:
- Use a detailed service manual for your specific engine.
- Take photos at every step to remember how everything fits back together.
3. Inspect and Clean Components
After disassembly, inspect each component for wear and damage. Pay special attention to:
- Cylinder walls: Check for scoring or wear that may require honing or boring.
- Pistons: Look for cracks, wear, or damage.
- Crankshaft: Inspect journals and check for scoring or out-of-round conditions.
- Valves and valve seats: Check for proper seating and wear.
- Bearings: Look for scoring, pitting, or wear in the main and rod bearings.
Use a micrometer to measure critical tolerances, such as cylinder bore diameter and crankshaft journal size. Clean all reusable components thoroughly using a parts washer, solvent, or degreaser.
4. Machine the Block (if necessary)
If the cylinder walls are significantly worn, the block may need to be machined by a professional. This can include boring the cylinders to a larger size or honing the walls to restore a smooth surface. The crankshaft may also need to be polished or ground down, and the main bearing surfaces should be checked for proper alignment.
5. Replace Worn Components
Now that the components have been cleaned and inspected, replace any worn or damaged parts. For most engine rebuilds, this includes:
- Pistons and rings: If the cylinder bores have been enlarged, oversized pistons may be necessary.
- Bearings: Replace the main and rod bearings with new ones from the rebuild kit.
- Gaskets and seals: Always use new gaskets and seals during reassembly to prevent leaks.
- Timing components: A new timing chain or belt is usually required.
6. Reassemble the Engine
Rebuilding is essentially the reverse of disassembly, but with a focus on precision and cleanliness. Use assembly lube on bearings, bolts, and other critical parts to prevent wear during initial startup.
- Install the crankshaft: Insert new bearings and torque the main caps to the manufacturer’s specifications using a torque wrench.
- Install pistons and rods: Use a piston ring compressor to install the pistons into the cylinders. Torque the rod bolts to the correct specification.
- Install the camshaft: If your engine has an overhead camshaft, install it along with the timing chain or belt, ensuring the timing marks are aligned.
- Reinstall the cylinder heads: Torque the head bolts in the correct sequence to ensure a proper seal.
- Reinstall manifolds and accessories: Reinstall the intake and exhaust manifolds, water pump, oil pan, and other components.
7. Reinstall the Engine in the Vehicle
Once the engine is fully assembled, it’s time to reinstall it in the vehicle. Use the engine hoist to carefully position the engine and bolt it back onto the mounts. Reconnect all hoses, wiring, and other components that were disconnected during removal. Finally, refill the engine with oil and coolant.
8. Initial Startup and Break-In
The first startup after a rebuild is critical. Here’s what you should do:
- Prime the oil pump: Crank the engine without starting it to build oil pressure and lubricate the engine’s internal parts.
- Check for leaks: Look for oil, coolant, or fuel leaks during the initial startup.
- Break in the engine: Follow the manufacturer’s recommended procedure for breaking in a new engine. This usually involves varying engine speed and load for the first few hundred miles to properly seat the rings.

Credit: www.streetmachine.com.au
Frequently Asked Questions
Here are some FAQs about rebuilding an engine –
1. How long does it take to rebuild an engine?
Rebuilding an engine can take anywhere from 20 to 50 hours, depending on your skill level, the condition of the engine, and the complexity of the rebuild. If you’re a novice, you may need more time to carefully follow each step.
2. What are the benefits of rebuilding an engine?
Rebuilding an engine extends the life of your vehicle, improves performance, and can be more cost-effective than purchasing a new engine. Additionally, it allows you to customize the build, optimizing for power, efficiency, or longevity.
3. Do I need special tools to rebuild an engine?
Yes, you will need specific tools such as a torque wrench, micrometer, piston ring compressor, and an engine hoist. Some specialized tools, like a cylinder honing tool, may require professional assistance.
4. How much does it cost to rebuild an engine?
The cost of rebuilding an engine varies widely, ranging from $500 to $3,000 or more, depending on the parts needed, whether you perform the work yourself, and if any machining is required. Labor costs at a shop could add significantly to the price.
5. Is it worth rebuilding an engine?
Rebuilding an engine is worth it if your car is in good overall condition and the rebuild will add years of reliable use. It’s a good option for those who want to maintain a specific vehicle or avoid the cost of buying a new one.
Conclusion
Rebuilding an engine is a complex but rewarding process that can breathe new life into an old vehicle. With the right tools, patience, and attention to detail, you can successfully rebuild your engine and enjoy years of improved performance. Whether you’re doing it for the first time or are a seasoned mechanic, the process offers a deep sense of accomplishment and a newfound appreciation for the heart of your vehicle.