To test a crankshaft position sensor, you’ll need a multimeter to check the sensor’s resistance and voltage output. Start by measuring the sensor’s resistance against the manufacturer’s specifications, and then test the voltage signal while the engine is cranking. If the readings are outside the specified range, the sensor may be faulty and need replacement.
The crankshaft position sensor (CKP sensor) is a vital component in your vehicle’s engine management system. It monitors the position and rotational speed of the crankshaft, providing crucial data to the engine control unit (ECU) to ensure proper ignition timing and fuel injection.
A faulty CKP sensor can lead to a range of issues, including engine misfires, stalling, and difficulty starting. Testing the CKP sensor is an essential diagnostic step when you suspect problems with your vehicle’s engine performance.
How to Test a Crankshaft Position Sensor
To test a crankshaft position sensor, you’ll need the following tools:
- Multimeter: A digital multimeter is essential for measuring the sensor’s resistance, voltage, and signal output.
- Oscilloscope (optional): An oscilloscope provides a visual representation of the sensor’s signal, which can be useful for more detailed diagnostics, particularly with Hall-effect sensors.
- Vehicle Service Manual: The service manual provides specific resistance values, wiring diagrams, and sensor locations for your vehicle model.
- Basic Hand Tools: Screwdrivers, wrenches, and sockets may be needed to access and remove the CKP sensor.
Steps to Test a Crankshaft Position Sensor
The testing process varies slightly depending on whether you have an inductive or Hall-effect CKP sensor. Below are the steps for testing both types.
1. Locate the CKP Sensor
- Consult the Service Manual: The CKP sensor is usually located near the crankshaft pulley, flywheel, or transmission bell housing. The exact location varies by vehicle make and model.
- Inspect the Sensor and Wiring: Before testing, visually inspect the sensor and its wiring for any signs of damage, corrosion, or loose connections.
2. Test the Inductive (Magnetic) CKP Sensor
Inductive sensors are the most common type found in older vehicles.
- Step 1: Set the Multimeter to Ohms (Ω): Set your multimeter to measure resistance. Disconnect the sensor’s electrical connector and place the multimeter leads on the sensor terminals.
- Step 2: Measure the Resistance: Compare the resistance reading with the specifications provided in the service manual. Typically, the resistance should fall within a range, often between 200 to 1,200 ohms.
- Step 3: Test the Output Signal: Reconnect the sensor and set the multimeter to measure AC voltage. With the engine cranking (but not starting), place the leads on the sensor terminals again. You should see a small AC voltage reading (often 0.2 to 2 volts). If there’s no reading or it’s outside the specified range, the sensor may be faulty.
3. Test the Hall-Effect CKP Sensor
Hall-effect sensors are common in newer vehicles and provide a digital output.
- Step 1: Set the Multimeter to DC Voltage: Disconnect the sensor’s electrical connector. Set your multimeter to measure DC voltage.
- Step 2: Check the Power Supply: With the ignition on (engine off), measure the voltage between the sensor’s power wire (usually red) and ground. You should see around 5 volts or 12 volts, depending on your vehicle.
- Step 3: Measure the Signal Output: Connect the sensor, and while cranking the engine, measure the voltage between the signal wire (usually green or white) and ground. The voltage should fluctuate between 0 volts and 5 volts (or 12 volts) as the sensor detects the crankshaft’s position.
- Step 4: Use an Oscilloscope (Optional): If you have an oscilloscope, connect it to the signal wire to observe the waveform. A healthy Hall-effect sensor will produce a consistent square wave pattern.
4. Interpret the Results
- Normal Readings: If the sensor produces the expected resistance and voltage readings, it’s likely functioning correctly. However, further testing may be needed if symptoms persist.
- Abnormal Readings: If the readings are outside the specified range, the CKP sensor is likely faulty and should be replaced. Also, check the wiring and connectors, as these can also cause similar symptoms.
5. Reassemble and Test the Vehicle
- Reinstall the CKP Sensor: If you removed the sensor for testing, reinstall it, ensuring it’s properly aligned and secured.
- Reconnect the Battery: If you disconnected the battery before testing, reconnect it and start the engine.
- Monitor Engine Performance: After testing and reassembling, monitor the engine for any persistent symptoms. If the issue is resolved, the CKP sensor was likely the problem. If not, further diagnostics may be required.
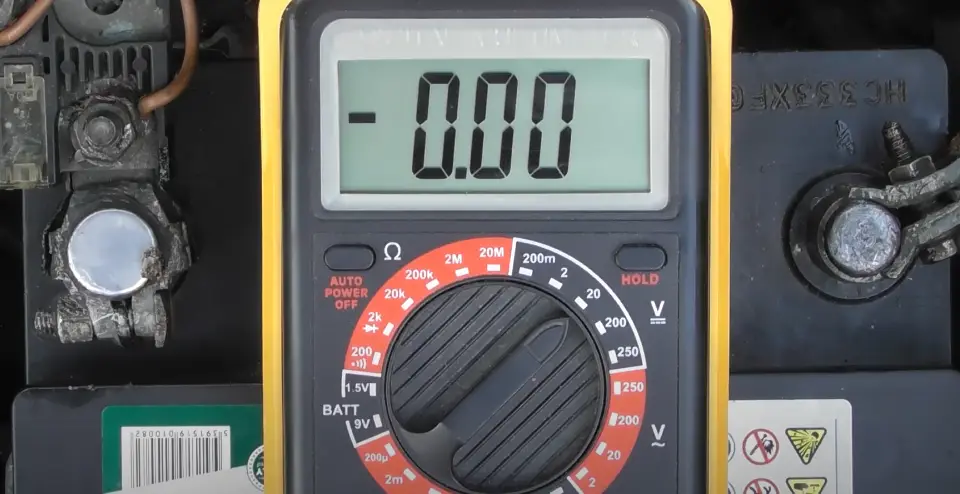
Frequently Asked Questions
Here are some FAQs about testing the crankshaft position sensor –
1. What are the symptoms of a failing crankshaft position sensor?
Symptoms of a failing CKP sensor include engine misfires, stalling, difficulty starting, rough idling, and the check engine light being illuminated. These issues occur because the ECU receives inaccurate data about the crankshaft’s position and speed.
2. Can I drive with a faulty crankshaft position sensor?
While it may be possible to drive with a faulty CKP sensor, it’s not recommended. A malfunctioning sensor can cause the engine to run poorly, increase fuel consumption, and even lead to engine stalling, which can be dangerous.
3. How often should I test the crankshaft position sensor?
The CKP sensor does not require regular testing as part of routine maintenance. However, if you experience engine performance issues or receive related fault codes, testing the sensor should be part of the diagnostic process.
4. Can a crankshaft position sensor be cleaned instead of replaced?
In some cases, the CKP sensor can be cleaned if it’s contaminated with oil or debris. However, if the sensor is physically damaged or testing reveals that it’s faulty, crankshaft position sensor replacement is necessary.
5. How much does it cost to replace a crankshaft position sensor?
The cost of replacing a CKP sensor varies depending on the make and model of your vehicle. On average, parts and labor can range from $100 to $250. However, prices can be higher for certain vehicles or if additional repairs are needed.
Conclusion
Testing the crankshaft position sensor is a crucial step in diagnosing engine performance issues. Whether you have an inductive or Hall-effect sensor, using a multimeter (and an oscilloscope if available) can help you determine if the sensor is functioning correctly. Regular testing and maintenance of the CKP sensor can prevent more serious engine issues and keep your vehicle running smoothly. If the sensor fails the tests, it’s advisable to replace it promptly to avoid further complications.