Blower motor bearing replacement is necessary when the bearings in the blower motor wear out, leading to noise and reduced efficiency in your vehicle’s HVAC system. The process involves removing the blower motor, replacing the worn bearings, and reassembling the motor. Proper maintenance, like regular cleaning and lubrication, can extend the life of the bearings and delay the need for replacement.
The blower motor is an essential component of your vehicle’s HVAC (heating, ventilation, and air conditioning) system, responsible for circulating air throughout the cabin. At the heart of the blower motor are the bearings, which allow the motor shaft to spin smoothly and efficiently. Over time, these bearings can wear out, leading to noise, reduced airflow, and eventually motor failure.
When this happens, replacing the blower motor bearings becomes necessary to restore the functionality of the HVAC system.
Contents
- 1 What Are Blower Motor Bearings?
- 2 Why Blower Motor Bearings Fail
- 3 Symptoms of Blower Motor Bearing Failure
- 4 Diagnosing Blower Motor Bearing Failure
- 5 Blower Motor Bearing Replacement: A Step-by-Step Guide
- 5.1 Tools and Materials Needed
- 5.2 Step 1: Prepare the Vehicle
- 5.3 Step 2: Locate and Remove the Blower Motor
- 5.4 Step 3: Disassemble the Blower Motor
- 5.5 Step 4: Remove the Old Bearings
- 5.6 Step 5: Clean the Motor Components
- 5.7 Step 6: Install the New Bearings
- 5.8 Step 7: Reinstall the Blower Motor
- 5.9 Step 8: Test the Blower Motor
- 6 Blower Motor Bearing Replacement Costs
- 7 Tips for Maintaining Blower Motor Bearings
- 8 Conclusion
What Are Blower Motor Bearings?
Blower motor bearings are small, yet crucial components located inside the blower motor. They support the motor shaft and reduce friction as it rotates, ensuring the motor runs quietly and efficiently.
Bearings are typically made from durable materials like steel or ceramic, designed to withstand the high speeds and continuous operation of the blower motor. However, like all mechanical components, they can wear out over time due to heat, friction, and environmental factors.
Why Blower Motor Bearings Fail
Several factors can contribute to the failure of blower motor bearings:
- Wear and Tear: Over time, the continuous rotation of the motor shaft can cause the bearings to wear down, leading to increased friction and eventually, failure.
- Lack of Lubrication: Bearings require proper lubrication to function smoothly. If the lubricant dries out or becomes contaminated, the increased friction can cause the bearings to wear out faster.
- Contamination: Dust, dirt, and moisture can enter the blower motor and contaminate the bearings, causing them to corrode or become clogged, leading to failure.
- Overheating: Excessive heat, either from the motor itself or from external sources, can cause the bearings to expand and lose their effectiveness, leading to failure.
- Imbalance: An imbalanced blower motor fan can place uneven stress on the bearings, causing them to wear out prematurely.
Symptoms of Blower Motor Bearing Failure
Recognizing the symptoms of blower motor bearing failure is crucial for timely repair and preventing further damage. Here are some common signs that your blower motor bearings may be failing:
- Squealing or Grinding Bearing Noise: One of the most common symptoms of failing blower motor bearings is a high-pitched squealing or grinding noise, especially when you first turn on the HVAC system or increase the fan speed.
- Reduced Airflow: If the blower motor bearings are failing, the motor may struggle to push air through the system, resulting in reduced airflow from the vents.
- Overheating Motor: Failing bearings can cause the blower motor to overheat, which may lead to a burning smell or even smoke coming from the vents.
- Vibration: An imbalanced motor due to bearing failure can cause noticeable vibration in the dashboard or HVAC controls.
- Inconsistent Fan Speeds: Bearing failure can cause the motor to operate inconsistently, leading to fluctuating fan speeds or the fan only working at certain speeds.
Diagnosing Blower Motor Bearing Failure
Before replacing the blower motor bearings, it’s essential to accurately diagnose the issue. Here’s how you can do it:
- Listen for Noise: Turn on your vehicle’s HVAC system and listen for any unusual noises. Pay attention to whether the noise changes with different fan speeds, as this can indicate the severity of the bearing issue.
- Inspect the Blower Motor: If you’re comfortable working on your vehicle, remove the blower motor from its housing and inspect it for signs of wear, damage, or contamination. Look for any visible signs of bearing damage, such as rust, debris, or wear marks.
- Check for Imbalance: Inspect the blower motor fan for any signs of damage or imbalance, such as bent blades or debris buildup. An imbalanced fan can put additional stress on the bearings, leading to failure.
- Test the Motor’s Electrical System: Use a multimeter to test the blower motor’s electrical connections and ensure that it’s receiving the proper voltage. An overworked or overheating motor might indicate bearing failure.
Blower Motor Bearing Replacement: A Step-by-Step Guide
Replacing blower motor bearings can be a complex task, but with the right tools and knowledge, it can be done by a skilled DIYer. Here’s a step-by-step guide to replacing the blower motor bearings:
Tools and Materials Needed
- New blower motor bearings (specific to your vehicle’s make and model)
- Screwdrivers (flathead and Phillips)
- Wrenches or socket set
- Bearing puller or extractor tool
- Lubricant (bearing-specific)
- Cleaning supplies (rags, compressed air, etc.)
- Service manual for your vehicle
Step 1: Prepare the Vehicle
Start by parking your vehicle on a flat surface and turning off the engine. Disconnect the battery to prevent any electrical shocks or accidental starts while working on the blower motor.
Step 2: Locate and Remove the Blower Motor
The blower motor is typically located under the dashboard on the passenger side of the vehicle. You may need to remove the glove box or other panels to access it. Once located, disconnect the electrical connector from the motor and remove any mounting screws or bolts holding the motor in place. Carefully remove the blower motor from its housing.
Step 3: Disassemble the Blower Motor
With the blower motor removed, you’ll need to disassemble it to access the bearings. This may involve removing the fan or impeller attached to the motor shaft. Use a wrench or socket set to carefully remove any retaining nuts or clips. Be mindful of the orientation of the components for reassembly.
Step 4: Remove the Old Bearings
Once the motor is disassembled, use a bearing puller or extractor tool to carefully remove the old bearings from the motor shaft. Be gentle to avoid damaging the shaft or surrounding components. Take note of the bearing size and type, as you’ll need this information when purchasing replacements.
Step 5: Clean the Motor Components
Before installing the new bearings, clean the motor components thoroughly. Use compressed air to remove any dust or debris from the motor housing, shaft, and surrounding areas. Ensure that all components are free of contaminants that could affect the performance of the new bearings.
Step 6: Install the New Bearings
Install the new bearings onto the motor shaft, ensuring they are seated correctly and securely. Apply a small amount of bearing-specific lubricant to help reduce friction and ensure smooth operation. Reassemble the motor by reattaching the fan or impeller and securing any retaining nuts or clips.
Step 7: Reinstall the Blower Motor
With the new bearings installed and the motor reassembled, place the blower motor back into its housing. Secure it with the mounting screws or bolts and reconnect the electrical connector. Ensure that all components are properly aligned and that there are no loose parts.
Step 8: Test the Blower Motor
Reconnect the battery and start the vehicle. Turn on the HVAC system and test the blower motor at different fan speeds. Listen for any unusual noises and check for proper airflow. If the motor operates smoothly and quietly, the bearing replacement was successful.
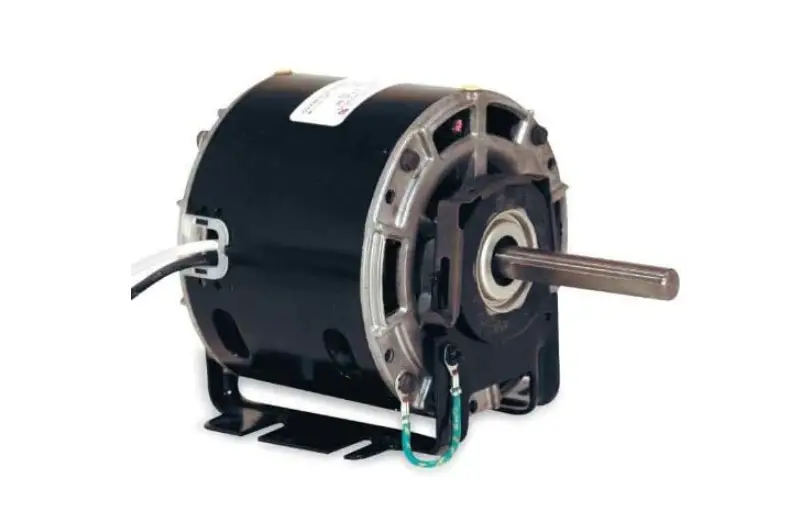
Read More: Replaced Blower Motor and Resistor Still Not Working
Blower Motor Bearing Replacement Costs
The cost of replacing blower motor bearings can vary depending on several factors, including the make and model of your vehicle, the availability of parts, and whether you perform the replacement yourself or hire a professional. Here’s a breakdown of potential costs:
- Bearings: High-quality blower motor bearings typically cost between $20 and $50, depending on the type and size required for your vehicle.
- Tools: If you don’t already have the necessary tools, purchasing or renting a bearing puller, socket set, and other tools could add $50 to $100 to your total cost.
- Labor: If you choose to have a professional mechanic replace the bearings, labor costs can range from $100 to $300, depending on the complexity of the job and the labor rates in your area.
- Replacement Blower Motor: In some cases, it may be more cost-effective to replace the entire blower motor assembly rather than just the bearings. A new blower motor typically costs between $100 and $300, depending on your vehicle’s make and model.
Tips for Maintaining Blower Motor Bearings
To extend the life of your blower motor bearings and avoid the need for replacement, consider the following maintenance tips:
- Regularly Replace the Cabin Air Filter: A clogged cabin air filter can restrict airflow and cause the blower motor to work harder, leading to premature bearing wear.
- Keep the HVAC System Clean: Periodically clean the blower motor and its components to prevent dust, dirt, and debris from contaminating the bearings.
- Lubricate Bearings as Needed: If your blower motor bearings are serviceable, ensure they are properly lubricated according to the manufacturer’s recommendations.
- Address Imbalance Issues Promptly: If you notice any vibration or imbalance in the blower motor fan, address the issue immediately to prevent damage to the bearings.
Conclusion
Blower motor bearing replacement is an important maintenance task that can restore the functionality of your vehicle’s HVAC system and prevent further damage. By understanding the symptoms of bearing failure, diagnosing the issue accurately, and following the correct steps for replacement, you can ensure that your blower motor operates smoothly and quietly.