Crankshaft bearings are typically made from materials like Babbitt metal, copper-lead alloys, aluminum alloys, tri-metal layers, and polymers. Each material is chosen for its specific properties, such as strength, wear resistance, and ability to handle high temperatures. The selection of material depends on the engine’s performance requirements and operating conditions.
Crankshaft bearings play a crucial role in the operation of an internal combustion engine. These bearings support the crankshaft and reduce friction between the rotating crankshaft and the stationary engine block, allowing the engine to run smoothly and efficiently. The materials used in the construction of crankshaft bearings are vital to their performance, durability, and longevity.
Contents
Crankshaft Bearings
Before exploring the materials, it’s essential to understand the function of crankshaft bearings. Crankshaft bearings are designed to handle the load of the rotating crankshaft and absorb the forces generated during engine operation.
They also help maintain proper oil clearance, ensuring a thin film of lubricant exists between the bearing surface and the crankshaft. This oil film is crucial in preventing metal-to-metal contact, which would otherwise lead to excessive wear, heat generation, and potential engine failure.
Types of Crankshaft Bearings
Crankshaft bearings are typically divided into two main categories:
- Main Bearings: These bearings support the crankshaft within the engine block, allowing it to rotate smoothly while maintaining its alignment.
- Connecting Rod Bearings: These bearings connect the crankshaft to the connecting rods, which, in turn, connect to the pistons. They facilitate the conversion of the pistons’ linear motion into the crankshaft’s rotational motion.
Both types of bearings require materials that can withstand high loads, resist wear, and operate effectively under high temperatures and varying conditions.
Common Materials Used in Crankshaft Bearings
Crankshaft bearings are typically made from a combination of materials, each chosen for its specific properties. The most common materials include:
- Babbitt Metal (White Metal):
- Composition: Babbitt metal is an alloy primarily composed of tin, with additional elements like copper and antimony to enhance its strength and wear resistance.
- Properties: Babbitt metal is known for its excellent conformability, meaning it can adapt to slight misalignments and imperfections in the crankshaft. It also has good embeddability, allowing small particles to become embedded in the bearing surface rather than causing damage. Babbitt’s low melting point and softness enable it to form a thin, sacrificial layer that protects the underlying bearing material.
- Applications: Babbitt metal is often used as a thin overlay on other bearing materials or as a lining in heavy-duty and high-performance engines.
- Copper-Lead Alloys:
- Composition: These alloys typically consist of a mixture of copper and lead, with copper being the primary component.
- Properties: Copper-lead alloys are known for their high strength, good thermal conductivity, and excellent fatigue resistance. They can withstand heavy loads and high temperatures, making them suitable for demanding engine conditions. However, they have lower conformability and embeddability compared to Babbitt metal.
- Applications: Copper-lead bearings are commonly used in high-performance and heavy-duty engines, where the bearings must endure extreme conditions.
- Aluminum Alloys:
- Composition: Aluminum alloy bearings are made from aluminum, often combined with silicon, copper, or tin to enhance their properties.
- Properties: Aluminum alloys offer a good balance of strength, durability, and corrosion resistance. They are lightweight and have excellent thermal conductivity, which helps dissipate heat generated during engine operation. Aluminum bearings also have good conformability and embeddability, although not as high as Babbitt metal.
- Applications: Aluminum alloy bearings are widely used in passenger vehicles, where the operating conditions are less extreme than in high-performance engines.
- Tri-Metal Bearings:
- Composition: Tri-metal bearings are constructed with three layers: a steel backing for strength, a copper-lead intermediate layer for load-bearing capability, and a thin Babbitt or aluminum overlay for conformability and wear resistance.
- Properties: Tri-metal bearings combine the advantages of different materials to provide excellent performance in a wide range of conditions. The steel backing offers structural support, the copper-lead layer handles high loads, and the Babbitt or aluminum overlay provides a conformable, low-friction surface.
- Applications: Tri-metal bearings are commonly used in high-performance and racing engines, as well as in heavy-duty applications where durability and reliability are critical.
- Polymer Bearings:
- Composition: Polymer bearings are made from advanced plastic materials such as PTFE (polytetrafluoroethylene) or PEEK (polyether ether ketone).
- Properties: Polymer bearings offer excellent wear resistance, low friction, and good thermal stability. They are also resistant to corrosion and can operate without lubrication in some cases. However, they may not be suitable for extremely high-load or high-temperature applications.
- Applications: Polymer bearings are used in specific applications where their unique properties are advantageous, such as in certain hybrid or electric vehicles, or in engines where traditional lubrication is challenging.
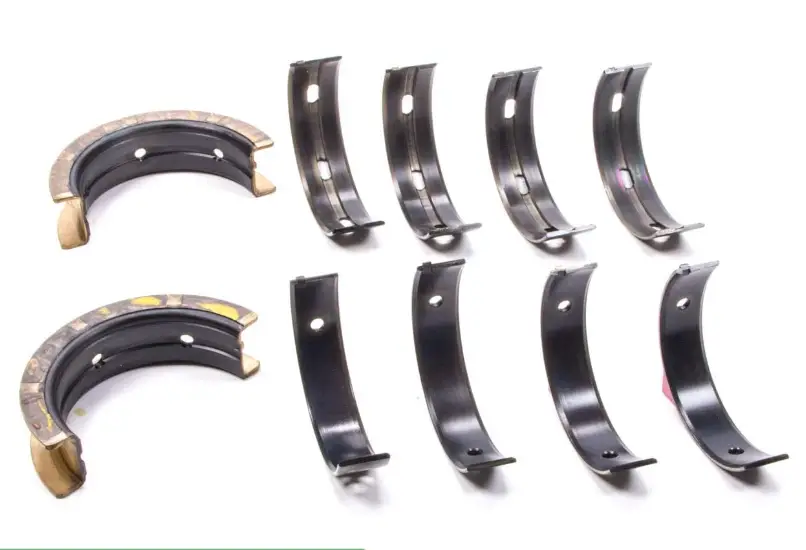
Factors Influencing Material Selection
The choice of material for crankshaft bearings depends on several factors:
- Engine Load and Performance Requirements:
- High-performance engines, such as those used in racing or heavy-duty applications, require materials that can withstand higher loads and temperatures. In these cases, copper-lead alloys or tri-metal bearings are often preferred.
- Operating Environment:
- The engine’s operating conditions, including temperature, speed, and load variations, influence material selection. For example, aluminum alloys may be chosen for engines that operate at moderate temperatures and loads, while Babbitt metal is favored for its conformability in environments with variable conditions.
- Cost Considerations:
- The cost of materials and manufacturing processes also plays a role in material selection. While tri-metal bearings offer superior performance, they may be more expensive to produce than simpler aluminum or copper-lead bearings.
- Manufacturing Techniques:
- Advances in manufacturing techniques, such as sintering and precision machining, have enabled the production of bearings with complex material compositions. These techniques allow for the creation of multi-layer bearings that optimize the performance of each material layer.
Importance of Proper Maintenance
Regardless of the material, proper maintenance is crucial to the longevity and performance of crankshaft bearings. Regular oil changes, using the correct type of oil, and maintaining proper engine operation are essential to preventing premature bearing wear and failure. Contaminants in the oil, improper installation, or excessive engine loads can lead to bearing damage, regardless of the material used.
Related Article
Can You Reuse Crankshaft Bearings?
Frequently Asked Questions
Here are some FAQs about the crankshaft bearing materials –
1. What are the most common materials used in crankshaft bearings?
The most common materials include Babbitt metal, copper-lead alloys, aluminum alloys, tri-metal bearings, and polymer bearings, each chosen for specific performance characteristics.
2. Why is Babbitt metal used in crankshaft bearings?
Babbitt metal is used for its excellent conformability, embeddability, and low friction properties, making it ideal for applications where slight misalignments or imperfections need to be accommodated.
3. What is the advantage of tri-metal bearings?
Tri-metal bearings combine the strengths of different materials, offering excellent load-bearing capability, durability, and conformability, making them suitable for high-performance and heavy-duty engines.
4. Can polymer bearings be used in high-performance engines?
Polymer bearings are generally not suitable for extremely high-load or high-temperature applications but may be used in specific cases where their properties, such as corrosion resistance, are advantageous.
5. How does the choice of crankshaft bearing material affect engine performance?
The choice of material impacts the bearing’s ability to handle loads, resist wear, dissipate heat, and maintain proper lubrication, all of which are crucial for optimal engine performance and longevity.
Conclusion
Crankshaft bearings are made from various materials, each selected for its specific properties to meet the demands of different engine applications. From Babbitt metal’s conformability to copper-lead alloys’ strength and tri-metal bearings’ combination of properties, these materials are designed to ensure the smooth and reliable operation of the engine. The selection of bearing material is influenced by factors such as engine load, operating environment, and cost, making it a critical decision in engine design and maintenance.