To remove stuck brake rotors, apply penetrating oil to the rotor-hub interface and use a rubber mallet to tap the rotor. If the rotor remains stuck, use a bolt to push it out from the back.
Brake rotors are a crucial part of the braking system, providing the friction surface for the brake pads to clamp onto, slowing down or stopping the vehicle. Over time, brake rotors can become rusted, stuck, or seized, making it challenging to remove them when it’s time for replacement or servicing. Whether you’re working on your car for regular maintenance or dealing with brake-related issues, knowing how to remove a stuck brake rotor is essential.
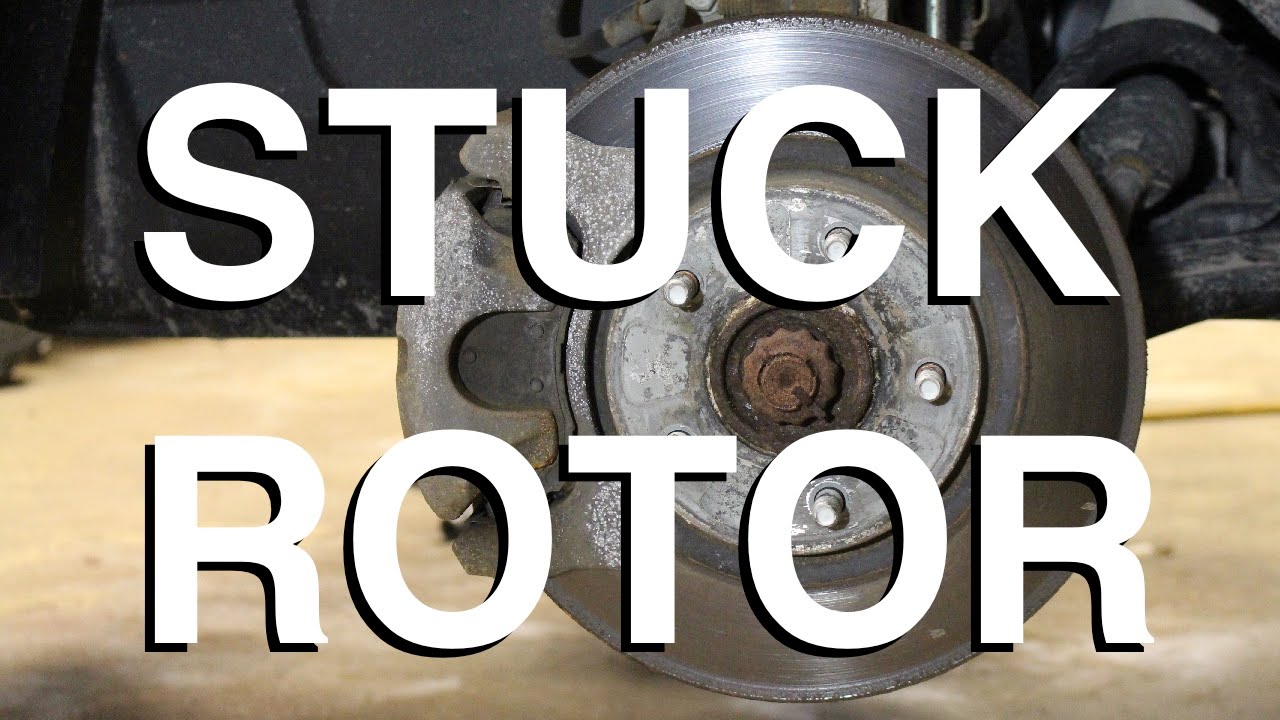
Contents
- 1 Why Do Brake Rotors Get Stuck?
- 2 Removing Stuck Brake Rotors
- 2.1 Step-by-Step Guide to Removing Stuck Brake Rotors
- 2.1.1 Step 1: Safety First
- 2.1.2 Step 2: Remove the Brake Caliper and Caliper Bracket
- 2.1.3 Step 3: Inspect the Rotor
- 2.1.4 Step 4: Apply Penetrating Oil
- 2.1.5 Step 5: Tap the Rotor with a Rubber Mallet
- 2.1.6 Step 6: Use a Sledgehammer (If Necessary)
- 2.1.7 Step 7: Use the Threaded Bolt Method (Optional)
- 2.1.8 Step 8: Remove the Rotor
- 2.1.9 Step 9: Clean the Hub
- 2.1.10 Step 10: Install the New Rotor
- 2.1 Step-by-Step Guide to Removing Stuck Brake Rotors
- 3 Frequently Asked Questions
- 4 Conclusion
Why Do Brake Rotors Get Stuck?
Brake rotors can become stuck to the hub assembly due to several factors:
- Rust and corrosion: Over time, moisture and road salt can cause rust to form between the rotor and the hub, especially in regions with harsh winters.
- Heat cycles: Repeated heating and cooling from braking can cause the rotor to expand and contract, creating a tight bond with the hub.
- Debris accumulation: Dirt, grime, and brake dust can build up between the rotor and the hub, making the rotor difficult to remove.
- Prolonged use: Leaving rotors in place for a long time without maintenance can cause them to seize, making them more challenging to dislodge.
Removing Stuck Brake Rotors
Before you begin the process, ensure you have the following tools and materials on hand:
- Lug wrench or breaker bar: To remove the wheel nuts.
- Socket set: To remove the caliper and other bolts.
- Ratchet wrench: For easier bolt removal.
- Pry bar: To help separate the rotor from the hub.
- Rubber mallet or sledgehammer: For tapping the rotor loose.
- Penetrating oil: To break through rust and corrosion.
- Threaded bolts (optional): Some rotors have threaded holes designed to help push them off the hub.
- Wire brush: To clean off rust and debris from the hub once the rotor is removed.
- Jack and jack stands: To lift and secure the vehicle safely.
- Safety glasses and gloves: For protection during the process.
Step-by-Step Guide to Removing Stuck Brake Rotors
Follow the steps below to do the job successfully –
Step 1: Safety First
Before you start working on your car, ensure your safety by following these steps:
- Park on a flat surface: Make sure the car is parked on a level surface and engage the parking brake.
- Loosen the lug nuts: Use a lug wrench or breaker bar to slightly loosen the lug nuts while the vehicle is still on the ground. Don’t remove them yet.
- Lift the vehicle: Using a jack, lift the car and secure it with jack stands for safety. Ensure the car is stable before proceeding.
- Remove the wheel: Once the car is lifted, fully remove the lug nuts and take off the wheel.
Step 2: Remove the Brake Caliper and Caliper Bracket
With the wheel off, you’ll have direct access to the brake rotor and caliper. You need to remove the caliper to get to the rotor.
- Unbolt the caliper: Use your socket set or ratchet wrench to remove the bolts holding the caliper in place. There are typically two bolts on the back of the caliper.
- Hang the caliper: Do not let the caliper hang by the brake line as this can damage the line. Use a piece of wire or a bungee cord to hang the caliper securely.
- Remove the caliper bracket: After removing the caliper, the caliper bracket is next. Remove the bolts holding the caliper bracket to the wheel hub. Once the bracket is off, you should have clear access to the rotor.
Step 3: Inspect the Rotor
With the caliper and bracket removed, you can now examine the rotor. In many cases, rust and debris around the hub will be the primary cause of the rotor being stuck.
- Look for threaded holes: Some rotors come with small threaded holes that can be used to push the rotor off the hub. If your rotor has these holes, you can use a matching bolt to screw into the hole, applying pressure and helping to release the rotor.
- Check for rust: Rust around the hub and rotor can prevent the rotor from coming off easily. Use penetrating oil around the center of the rotor to help break up the rust.
Step 4: Apply Penetrating Oil
Spray penetrating oil around the rotor’s center hub and the edges where it meets the hub. Let the oil soak for a few minutes, allowing it to penetrate the rust and corrosion.
Step 5: Tap the Rotor with a Rubber Mallet
After applying the penetrating oil, use a rubber mallet to gently tap around the edges of the rotor. This can help to loosen the rotor from the hub without causing damage.
- Work in a circular motion: Start by tapping the rotor lightly in a circular motion. If the rotor doesn’t move, increase the force gradually.
- Avoid hitting the rotor face directly: Try not to hit the rotor’s braking surface too hard, as this could damage it if you plan to reuse it.
Step 6: Use a Sledgehammer (If Necessary)
If the rubber mallet doesn’t do the trick, you can use a sledgehammer. However, be cautious with this method as hitting the rotor too hard can damage surrounding components.
- Hit the rotor from behind: Stand behind the rotor and hit the back of the rotor with the sledgehammer. Use short, controlled swings.
- Rotate the rotor as you hit: Strike the rotor in multiple spots to distribute the force and prevent it from warping.
Step 7: Use the Threaded Bolt Method (Optional)
If your rotor has threaded holes designed for removal, insert the correct size bolt into the holes and gradually tighten them. This will push the rotor away from the hub. Tighten each bolt evenly to avoid damaging the rotor or hub.
Step 8: Remove the Rotor
Once the rotor is loose, carefully slide it off the hub. If it’s still stuck, repeat the previous steps—adding more penetrating oil, tapping with a mallet, or using the sledgehammer.
Step 9: Clean the Hub
After removing the rotor, use a wire brush to clean the hub surface. Removing rust and debris will help ensure the new rotor sits flush and prevents future seizing.
Step 10: Install the New Rotor
Once the hub is clean, you’re ready to install the new rotor or reinstall the old one if it was simply stuck and not damaged. Follow the reverse process to reinstall the caliper bracket, caliper, and wheel.
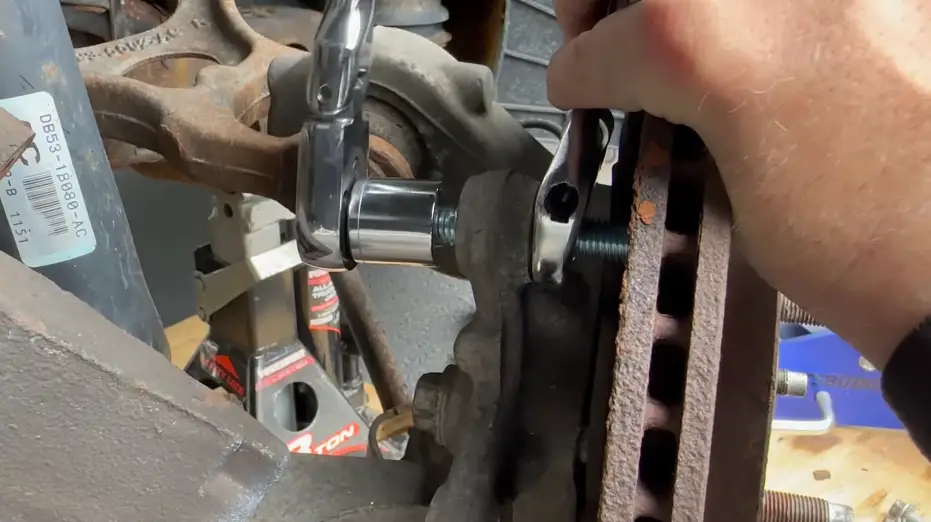
Frequently Asked Questions
Here are some FAQs about the removing a stuck rotor –
1. Can I use heat to remove a stuck rotor?
Yes, applying heat using a propane torch around the hub area can expand the metal and help break the bond between the rotor and hub. However, be cautious when using heat near sensitive components like brake lines.
2. Is it safe to hit the rotor with a sledgehammer?
While using a sledgehammer can be effective, it should be done carefully. Use controlled strikes and aim for the rotor’s backside to avoid damaging the hub, studs, or other parts.
3. How do I prevent my brake rotors from getting stuck again?
To prevent rotors from sticking in the future, apply anti-seize lubricant around the hub area during installation. Regular brake maintenance and cleaning can also help reduce rust and debris buildup.
4. What if the rotor won’t come off even after hitting it?
If the rotor is still stuck after trying the recommended methods, check for any rotor retaining screws (small screws holding the rotor in place) that you may have missed. In rare cases, extreme rust may require professional help.
5. How do I know when my brake rotors need replacing?
Signs that your brake rotors need replacing include warping (causing vibration when braking), deep grooves, excessive rust, and scoring on the surface. Additionally, if the rotor thickness falls below the manufacturer’s recommended minimum, it should be replaced.
Conclusion
Dealing with stuck brake rotors can be frustrating, but with the proper approach, it’s a task that can be tackled confidently. Understanding why rotors get stuck-whether due to rust, debris, or heat cycles-is key to choosing the right removal method.